Glue Anchor®
1. Outline
The "Glue Anchor®" is the brand-new method that fastens urethane foam, which is the cushion material for the seat, and the trim cover (skin material) that occupant physically touch on.
As shown in the figure below, the conventional method of fastening urethane foam and trim cover is
It was a "C-ring" construction method. The C-ring method fastens a core wire embedded in the urethane foam and the trim cord sewn to the trim cover with an iron ring called a C ring.
The "Glue Anchor®" method, the world’s first technology is to fasten only the sewing line of the trim cover with an adhesive.
2. Benefits
- It is possible to experience the original suppleness of the skin material
- It is possible to make a sheet rich in design such as expressing unevenness on the sheet surface.
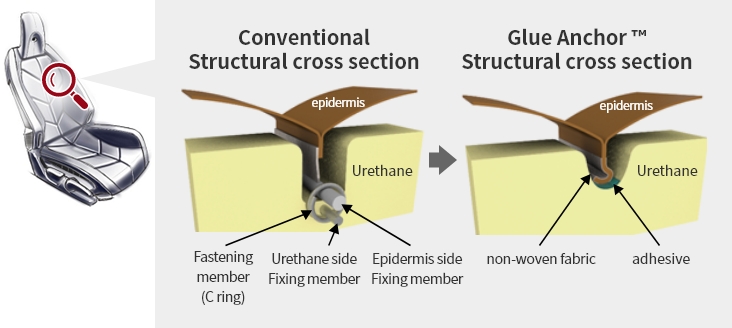
3. Reduction of CO2 emissions
Reduction in the amount of iron and resin used compared to the conventional, contributing to weight reduction
Laser welding
1. Outline
Laser welding is a method of melting (melting) metal using laser light as a heat source and joining.
It is adopted as a technology for joining parts used in seat frame.
2. Benefits
- Reduction of processing time by high-speed welding
- Realization of thinning by low heat input welding (lightening)
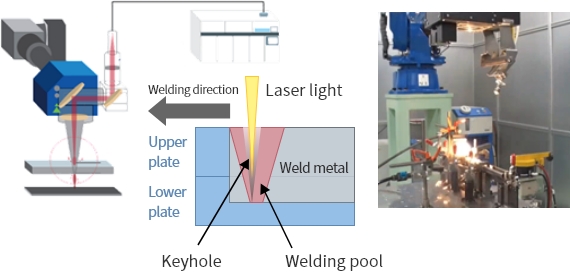
3. Reduction of CO2 emissions
Introduction of laser welding with low CO2 emissions
Welding length of TTK-X is reduced by 90% compared with TTK-1 with arc welding, making the amount of electric consumption less by 55%
Expansion of laser welding adoption: Significant reduction in power consumption
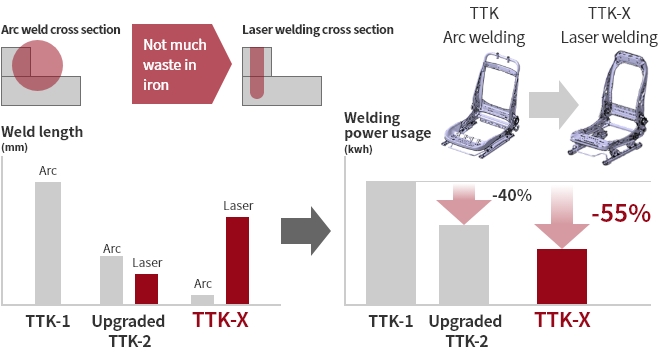
Integrated foaming method
1. Outline
The integrated foaming method is a method in which a frame and a cover are set in a mold, a polyurethane solution is
injected into the set cover, and "integrated foaming" is performed.
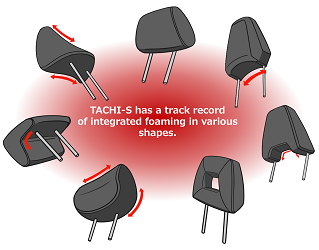
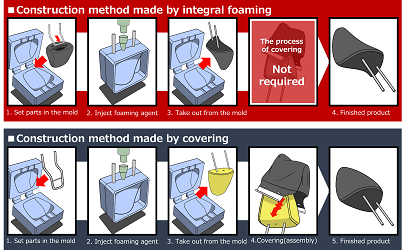
2. Benefits
- The process (labor) such as covering polyurethane can be saved.
- Increase in design freedom
3. Technology / strengths (simulation)
Build an integrated foam simulation technology,
Feasibility can be examined at the digital stage,
It is now possible to predict defects in advance. As a result, it is possible to reduce the production loss of foam molds and the man-hours required to remake products.
In addition, our integrated foam simulation is used not only for headrest but also for improvement in
CAE accuracy of the entire automobile seat by taking over each data information.
Simulation of integrated foam method is feasible using soft-touch trim cover material
Process simulation
1. Outline
Process simulation is a digital tool of the process design, which is the main business of the Production Engineering Department.
As the term “3 Actuals” principles suggests, it is extremely important to confirm Actual reality, Actual sight and Actual thing.
However, as the development period of automobiles is becoming increasingly shorter,
Digital process simulation is essential to detecting problems at an early of the development.
2. Benefits
By inputting the information on work procedures, workers, incidental equipment, transportation equipment, layout In addition to 3D CAD data of jigs and tools and equipment
we can create virtual factory that moves as an animation. As a result, it allows us to find troubles at much earlier time than today, contributing to a decline in the amount of rework .
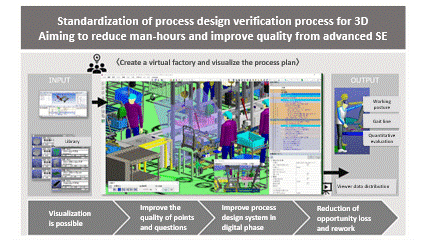
3. Technology and strengths
In a discussion with a veteran engineer, a young engineer can convey his/her views in word that are often found to be difficult to verbally communicate by using process simulation.
It also makes it possible to promote constructive discussion in diverse opinions among team members. We continue to use this tool as a new way of working.
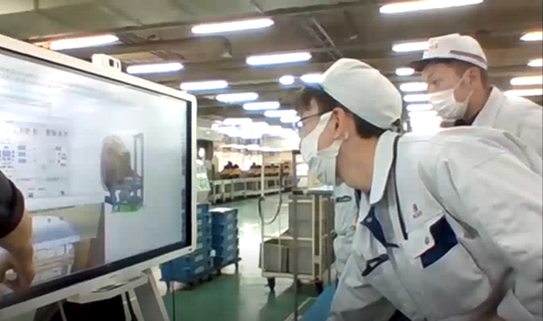