To Enhance Customer Satisfaction
To enable us to always meet our customers’ needs, we gather information regarding their requests and concerns and, in addition to fulfilling their conventional quality requirements and existing needs, aim to further enhance customer satisfaction by offering high quality products that meet their potential needs (inspirational quality).
Basic Approach to Enhancement of Customer Satisfaction
Guided by our Corporate Philosophy, “We deliver an inspirational experience to our customers worldwide through our technology and contribute to society as a brand you can trust”, we pursue manufacturing that leverages our strengths in the global pursuit of integrated manufacturing, from development to production, to develop and deliver products that meet the expectations and requirements of customers worldwide who sit on our seats.
Framework for the Enhancement of Customer Satisfaction
We have established separate organizations that engage in manufacturing for each of our major customers. Leveraging our strength as an independent and using design concepts that allow us to standardize our customers’ diverse needs to the maximum extent, we work as a united organization from the early stages to promote proposal activities that offer value that exceeds customers’ expectations.
In our Business Division, we share our customers’ latest needs globally at monthly Regional Marketing Meetings.
In addition, in sales strategy meetings, the Business Division shares information and discusses specific measures for development and production with the monozukuri Division.
Unified organizational sales activities to enhance customer satisfaction
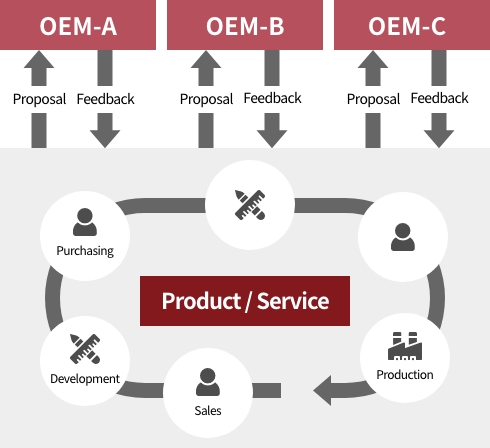
The Development Division regularly reports on the state of progress of new product development (quality, design, process review), including preparations from the pre-order stage to order placement and the launch of manufacturing processes.
In addition, we hold Strategy consideration meeting to consider proposals for new products and technologies for customers at any time. At the meeting, reports on the development of new products and technologies are presented, while the Business Division deliberates and reports on proposals to meet customer needs.
Development framework for enhancement of customer satisfaction
Efforts to Enhance Customer Satisfaction
To enhance customer satisfaction, TACHI-S believes that the clear identification of information regarding customers’ needs is key.
In addition to presenting our new products and technologies to our existing customers, We hold product exhibitions and technical presentations to give new customers the opportunity to get to know us. We also use such exhibitions as opportunities to seek out customers’ opinions and requirements.
With “Supporting People and the Earth through Seating Technology” as our corporate purpose, we are working on the evolution of products and technologies for the future.
In the area of “seating technology,” we aim to expand the freedom of appearance and form and to reduce weight with products that use body sensing and mechanisms that have no physical switches and instead work by sensing human movement and intentions.
In terms of “supporting people,” on the premise of rideshare scenarios, we will enhance customer experience value through the provision of spaces in which passengers can work or enjoy their privacy while riding in the vehicle, without being conscious of others.
To “supporting the Earth,” we will aim to reduce CO2 emissions by shifting away from petroleum-based materials and materials made with petroleum-generated energy to materials that are made with natural energy.
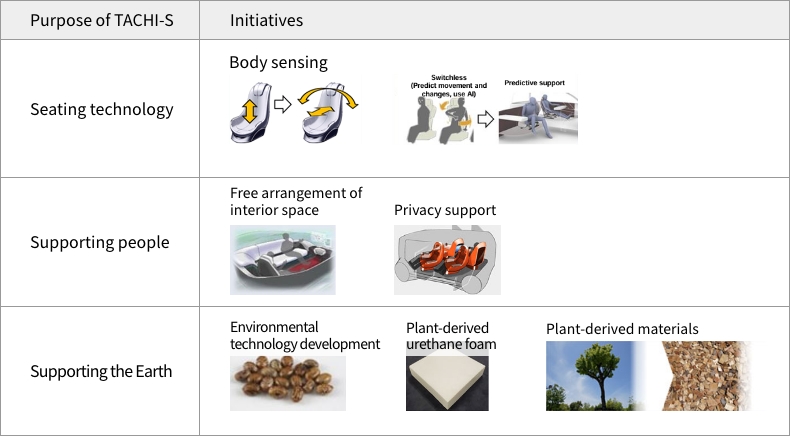
Quality Assurance and Quality Control
Basic Approach to Quality Assurance and Quality Control
Guided by the Corporate Philosophy of “To live in harmony with individuals and society and to put smiles on people’s faces by continuously creating living spaces of comfort and enrichment” TACHI-S has pursued quality assurance under the following quality policy, with the aim of realizing not only the quality that customers require, but also “inspirational quality,” which will meet potential needs that even customers themselves are not aware of.By sharing this policy across the entire TACHI-S Group in 14 countries around the world, we work as a united force to enhance customer satisfaction and provide trusted and inspirational products to customers the world over.
Quality Policy
Provide products that inspire confidence and excitement in customers, with a strong commitment to quality first and foremost.
Quality Assurance System
We implement monozukuri under an integrated system from design engineering and development to production. Through quality assurance activities conducted by integrated collaboration among all relevant departments for all quality processes, from product planning and design engineering to process design and management, we strive to provide products that respond to customers’ trust.
Quality Management Systems
To continue to provide inspirational products to customers, we work to spiral up quality with our quality management systems and the PDCA (P: Plan, D: Do, C: Check, and A: Action) cycle.
To achieve better quality, TACHI-S has obtained certification under ISO 9001, the international standard for quality management systems, and IATF 16949, the international standard for quality management systems in the automotive industry.
Quality management system standard certificates
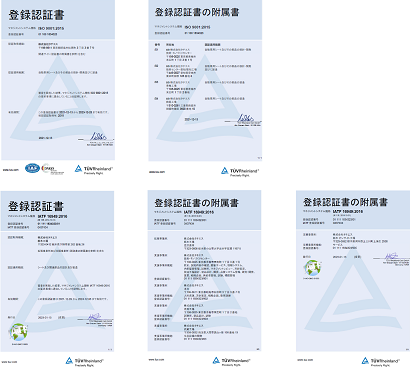
locations that have obtained quality management system certifications
Quality Assurance Process
In response to customer requests, we design quality into our products from the development stage and strive to improve and enhance quality through each individual process.
Major quality assurance activities
Process |
Quality Assurance Activities |
Production Development Stage |
Multifunctional teams (comprised of members from individual sections) are established to implement quality control for new products. These teams consider the various risks associated with products, as well as safety, functionality, performance, legal compliance and other factors, to design in quality that meets consumers’ requirements and expectations. |
Design Engineering and Prototyping Stage |
We strive to achieve quality in design engineering by confirming the appropriateness and feasibility of measures and policies for design issues, based on design reviews (verification and evaluation) of design engineering. |
Production and Prototyping Stage |
We conduct design reviews (verification and evaluation) of processes and strive to achieve the product quality that our customers require through process design (equipment layout), process management (establishment of rules), and thorough compliance with those rules. |
Mass-production Stage |
We pursue thorough site management to provide excellent products to customers. |
Quality assurance process
Efforts to Raise Quality Awareness and Improve Employees’ Skills
Our quality is supported by every individual engaged in individual processes, such as product development and manufacturing. To provide high-quality products, TACHI-S engages in company-wide efforts to develop and nurture employees' quality control capabilities. In addition to self-directed and mutual development through voluntary quality control activities in the workplace, we aim to create a vibrant workplace in which kaizen activities are ongoing, which we hope will lead to the enhancement of customer satisfaction and contribute to society.
Initiatives for enhancement of employees’ quality awareness and capabilities
Activity |
Description |
QC Circle activities |
Activities based on QC concepts and methods with the aim of continuous improvement of “quality” of work (products and services). |
Global Skills Contest |
This initiative aims to enhance monozukuri capabilities and to further improve technical abilities by having employees compete with each other with their skills. |
Participant comment
Japan Region QCC Contest (FY2019)
QCC activities have nurtured our kaizen abilities, resulting in more lively communication within our department.
Global QCC Contest (FY2018, Guangzhou, China)
Participating in the Global QCC Contest gave me the opportunity to talk to other participants from overseas locations face-to-face, which gave me a sense of solidarity and the feeling that we are all colleagues with the same purpose.
Scenes from Global Skills Contest and Contest winners (FY2018, Japan)
This global exchange of skills has helped to improve my own technical abilities. It was great to see the skills of the representatives of different locations up close.
Product Safety Assurance
Below are some examples of products and services by our company and affiliated companies that contribute to creating social value.
Approach to monozukuri that Positions Safety as the Top Priority
In addition to compliance with the laws and regulations of individual countries, TACHI-S conducts product developmentthat meets the strict safety evaluation criteria of our customers, the automotive manufacturers.
The most important factor in ensuring seat safety is design engineering that ensures safety in collisions. For minor collisions, curbing the deformation of the seat frame(*) is needed, but for serious collisions, by allowing the seat frame to crumple, the seat frame will absorb the energy generated by the collision. This minimizes the crash energy that is passed onto the passengers, thus protecting the passengers’ safety.
In the design engineering of seats, while taking the balance between those two scenarios into consideration, we actively pursue the development and introduction of new technologies for the light weighting of seats and the enhancement of seat comfort.
(*): The seat frame is the underframe component of an automotive seat.
Monozukuri System that Positions Safety as the Top Priority
The development and manufacture of automotive seats comprises the following processes. Many related divisions work together to ensure product safety.
In particular, as development timeframes have become shorter in recent years, safety analysis using simulation technology and design engineering feedback have become more important. TACHI-S strives to ensure product safety through various processes, including final safety assessment and confirmation through crash tests and frequent quality checks in the manufacturing process.
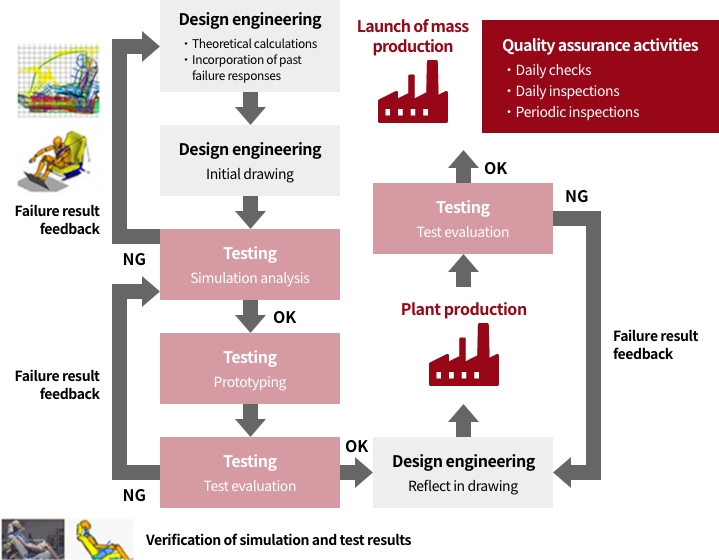
- Initial design engineering stage: Build basic design based on theoretical calculations and past failure information
- Simulation analysis stage: Conduct safety performance-specific assessments
- Prototype testing stage: Conduct actual crash tests with prototype model to verify appropriateness of design quality
- Mass-production testing stage: Conduct actual crash tests with samples equivalent to mass-production product to verify appropriateness of manufacturing quality
- Post mass-production launch: Conduct quality testing on products at manufacturing plant to confirm they are of predetermined quality
Efforts to Strengthen Global Systems to Ensure Product Safety
With the aim of the speedy development of safe, high-quality products to answer the needs of our customers around the world, we own product safety testing facilities in four locations—Japan, China, United States, and Mexico. The facilities in Japan, China, and Mexico are equipped with cutting-edge crash test equipment. We also own various types of crash dummies to comply with laws and regulations, the safety evaluation criteria of individual countries, and the evaluation requirements of automotive manufacturers, and we have established a global system for the speedy development of safe, high-quality products.
Crash test facilities and their development
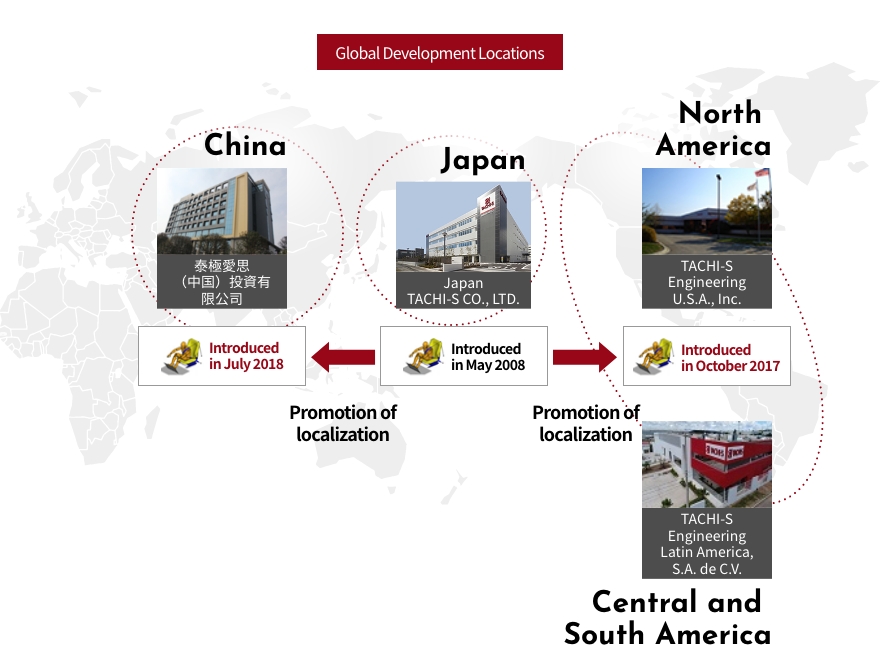
Crash test scenes
Responses to Product Problems
In the event of problems with our products, we promptly gather information from the customer and communicate the necessary information to the relevant departments. After that, while responding to the customer immediately, the relevant departments (including top management if necessary) gather in a Quality Meeting to analyze the problem based on gogen-shugi principles—GENba (actual location), GENbutsu (actual item), GENjitsu (actual facts), GENri (general principle) and GENsoku (general rule)—and undertake kaizen activities.
Flow of product problem response
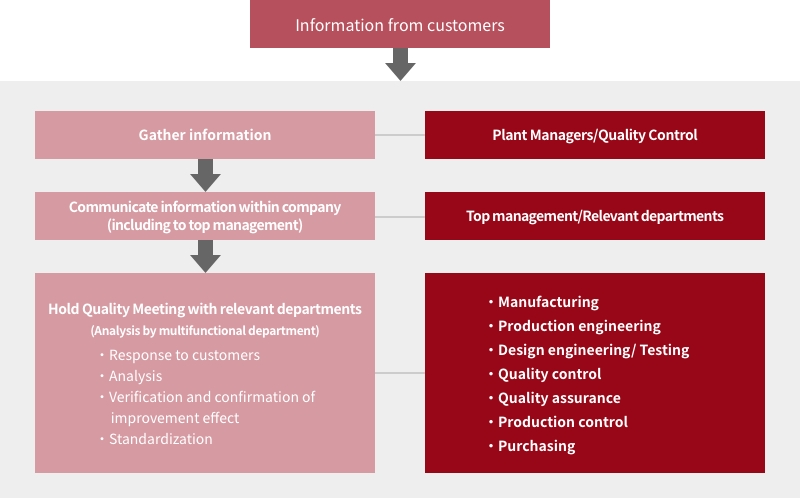